What is Porosity in Welding: Usual Resources and Efficient Remedies
What is Porosity in Welding: Usual Resources and Efficient Remedies
Blog Article
The Science Behind Porosity: A Comprehensive Guide for Welders and Fabricators
Recognizing the complex mechanisms behind porosity in welding is essential for welders and fabricators making every effort for flawless craftsmanship. From the structure of the base products to the details of the welding process itself, a multitude of variables conspire to either intensify or relieve the existence of porosity.
Comprehending Porosity in Welding
FIRST SENTENCE:
Assessment of porosity in welding exposes essential understandings into the integrity and quality of the weld joint. Porosity, identified by the visibility of dental caries or gaps within the weld steel, is a common issue in welding procedures. These voids, if not correctly addressed, can compromise the architectural honesty and mechanical residential or commercial properties of the weld, leading to potential failures in the ended up product.
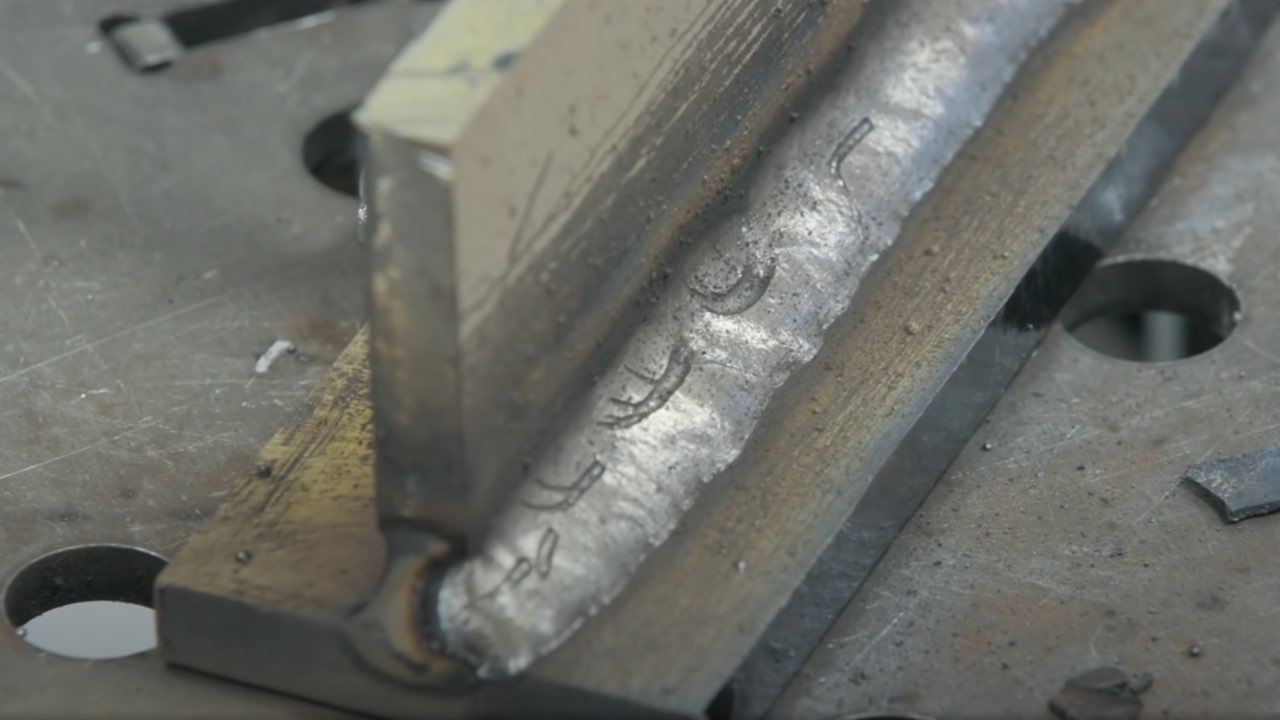
To find and quantify porosity, non-destructive testing methods such as ultrasonic testing or X-ray evaluation are typically utilized. These strategies permit the recognition of inner defects without endangering the integrity of the weld. By examining the size, shape, and distribution of porosity within a weld, welders can make enlightened decisions to boost their welding procedures and achieve sounder weld joints.

Elements Influencing Porosity Development
The incident of porosity in welding is influenced by a myriad of variables, ranging from gas securing effectiveness to the ins and outs of welding parameter setups. One vital factor adding to porosity formation is inadequate gas shielding. When the securing gas, normally argon or CO2, is not successfully covering the weld swimming pool, atmospheric gases like oxygen and nitrogen can contaminate the molten steel, resulting in porosity. Furthermore, the sanitation of the base products plays a considerable function. Contaminants such as corrosion, oil, or moisture can vaporize throughout welding, creating gas pockets within the weld. Welding criteria, consisting of voltage, existing, take a trip rate, and electrode type, also influence porosity development. Using inappropriate setups can generate too much spatter or heat input, which in turn can lead to porosity. In addition, the welding technique utilized, such as gas metal arc welding (GMAW) or protected steel arc welding (SMAW), can affect porosity formation because of variations in warmth circulation and gas insurance coverage. Comprehending and regulating these factors are necessary for lessening porosity in welding operations.
Effects of Porosity on Weld High Quality
The visibility of porosity likewise weakens the weld's resistance to corrosion, as the trapped air or gases within the voids can react with the surrounding environment, leading to deterioration over time. Additionally, porosity can hinder the weld's capacity to withstand pressure or impact, additional endangering the overall quality and dependability of the welded structure. In vital applications such as Go Here aerospace, vehicle, or structural building and constructions, where security and resilience are vital, the detrimental effects of porosity on weld high quality can have severe repercussions, highlighting the relevance of reducing porosity through correct welding methods and procedures.
Techniques to Lessen Porosity
Additionally, making use of the proper welding criteria, such as the appropriate voltage, existing, and take a trip speed, is crucial in protecting against porosity. Keeping a try this web-site constant arc size and angle throughout welding also aids reduce the likelihood of porosity.

Furthermore, selecting the appropriate protecting gas and keeping appropriate gas flow rates are necessary in decreasing porosity. Using the proper welding technique, such as back-stepping or employing a weaving motion, can also assist disperse warmth equally and minimize the chances of porosity development. Finally, guaranteeing proper ventilation in the welding setting to remove any type of potential sources of contamination is vital for attaining porosity-free welds. By implementing these strategies, welders can effectively reduce porosity and create high-quality welded joints.
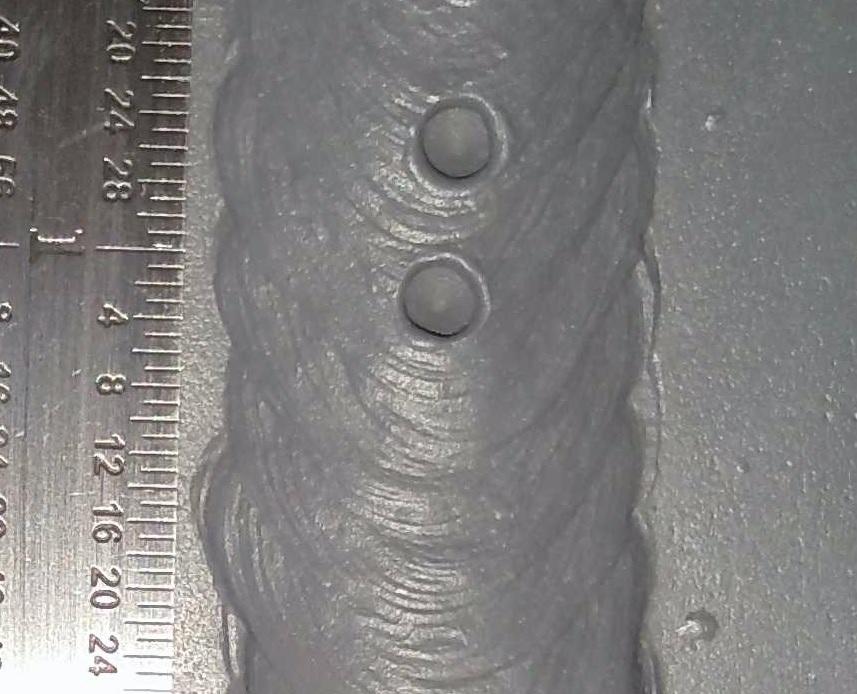
Advanced Solutions for Porosity Control
Applying innovative innovations and cutting-edge approaches plays a critical role in attaining remarkable control over porosity in welding processes. One innovative remedy is using advanced gas mixtures. Securing gases like helium or a blend of argon and hydrogen can aid lower porosity by providing far better arc stability and boosted gas protection. In addition, using sophisticated welding methods such as pulsed MIG welding or changed ambience welding can additionally assist alleviate porosity problems.
An additional advanced solution entails the usage of innovative welding equipment. Using devices with built-in features like waveform control and innovative power sources can improve weld high quality and decrease porosity threats. The execution of automated welding systems with accurate control over specifications can substantially minimize porosity problems.
Furthermore, including innovative monitoring and evaluation modern technologies such as real-time X-ray imaging or automated ultrasonic testing can assist in spotting porosity early in the welding process, enabling prompt restorative activities. Overall, incorporating these advanced options can significantly boost porosity control and boost the overall top quality of welded parts.
Verdict
In conclusion, understanding the science behind porosity in welding is essential for welders and makers to generate high-quality welds - What is Porosity. Advanced options for porosity control can additionally enhance click here for more the welding procedure and make certain a solid and dependable weld.
Report this page